Fiber drum producing facilities are required to take additional measures to clean new units for customers in the food, pharmaceutical and specialty chemical industries. Until recently, the Large Packaging Chicago Fiber facility met the higher hygiene standards by manually wiping top chimes and vacuuming the interior of each fiber drum produced.
In 2018, the drum cleaning process at Chicago Fiber was recognized as an area for potential ergonomic and automation improvement. Associates performing drum cleaning in the facility’s Clean Room were subjected to highly manual repetitive motion, which is a risk to the employees’ health. Automation of this task would increase the consistency of the drum cleaning and eliminate the repetitive motion performed by employees.
Because an automated technology which would meet our higher hygiene requirements was not available, the business set out to find a solution. After consultation with several external engineering firms, the Chicago Team selected Applied Manufacturing Technologies (AMT) from Orion, Michigan as the automation partner tasked to design and install the cleaning device. A commitment to a turn-key installation was primary in the selection of AMT for the design criteria deliverables.
In early October 2018, an AMT design team and the Mauser Packaging Solutions team initiated the kick off of the Clean Room Automation build. The teams met on a weekly basis to monitor project progress and address build issues for this new technology.
The Chicago Team was present for the run-off at AMT’s Design Center on April 12. Final installation of the Clean Room Automation at Chicago Fiber was completed by AMT on May 2 with sign-off by the MPS Project Team and Chicago Fiber Plant Manager Alfonzo Dubois.
The project met the manual content objective of eliminating repetitive motion activities and was completed within the CAPEX budget with the return on investement projected at less than one year.
The automation was designed with redundant Safety Guarding devices including physical barriers with interlocks, light curtains and motion sensor floor mats. AMT developed standard works for operation as well as Risk Assessment modules for repair and maintenance activities.
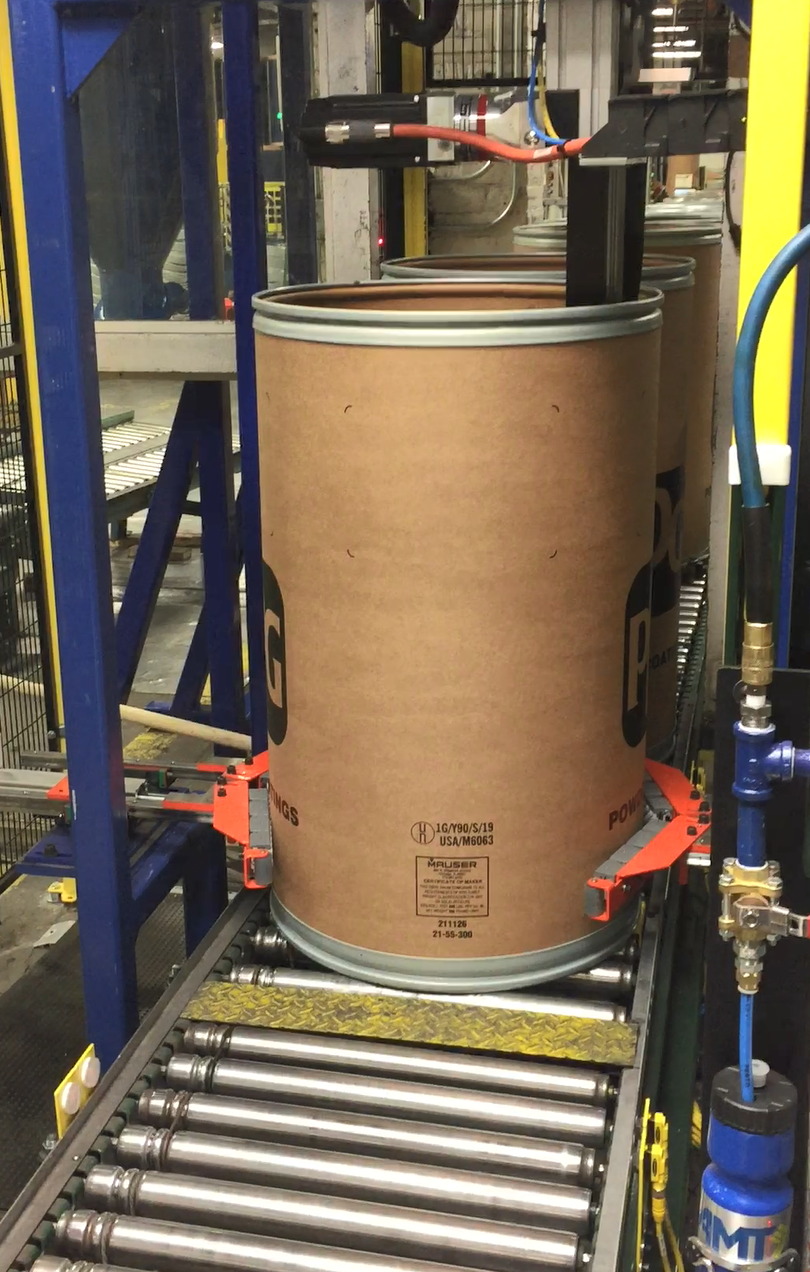
The Mauser Packaging Solutions team for this project was led by Andy Rutkowski, Divisional Quality Manager; Andrew Peldunas, Divisional Engineering Manager; Pat Ruggerio, NALP Electrical Safety Manager; and John Dergentis, NALP Fiber Business Unit Vice President and General Manager. In addition to this project, Engineering and Plant Management teams in all Large Packaging divisions are working on dozens of other projects to eliminate repetitive.
I am thankful for this team’s dedication to this project and their commitment to making our production work environment safer for our employees.