The 5S system is a lean manufacturing tool that improves workplace efficiency and eliminates waste. By providing a systematic framework for organization and cleanliness, 5S helps facilities avoid lost productivity from delayed work, unplanned downtime, and unsafe conditions.
There are five steps in the system that should be followed in sequential order:
SORT
Sort calls for a full assessment of materials and the keeping of only items essential for completing tasks. All items in a work area should be identified and unnecessary items removed.
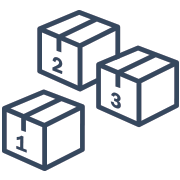
Set in Order
Set in order organizes items that survived Sort stage in a way that makes tasks easier to complete. Organize tools and materials in a clearly defined way that improved efficiency. Implement visual organization to streamline workflow and reduce waste.
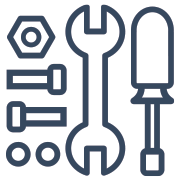
Shine
Shine requires a proactive effort be taken to keep workplace areas clean and orderly. Work areas, equipment and tools should be cleaned, and sources of contamination should be identified and eliminated.
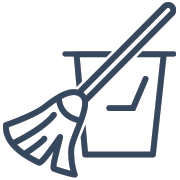
Standardize
Create and post rules for each work area that ensure the practices of the first 3S’s continue on a regular basis. Standards should be simple and visual. Assign tasks and create schedules so that everyone knows their responsibilities.
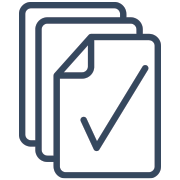
Sustain
Sustain ensures 5S is a long-term best practice rather than a brief experiment. Take steps to maintain processes and standards. Periodically perform audits on work areas to ensure 5S practices are being maintained.
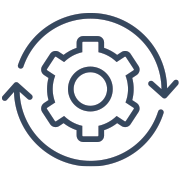
When it comes to lean manufacturing and workplace improvement, 5S is one of the most widely known and used lean tools. This is no surprise since 5S can increase workplace efficiency, reduce costs, and improve quality. But with many lean programs, it’s easy to focus only on the goals, and lose sight of the human factor. Worker safety is critical. That’s why many facilities add another step to the 5S cycle - Safety.
Unlike the first five steps, Safety is not a sequential step. It must be considered during each of the other steps. Choosing to implement the sixth “S”, Safety, can help improve workplace organization and efficiency, while also making the workplace safer.
Implementing the 5S system, with a continuous mindfulness of safety, can increase workplace efficiency, reduce cost, and improve quality while creating a better work environment for employees.