As we conclude Mauser Packaging Solutions’ 2021 Safety Month, we acknowledge that our commitment to safety is bigger than a one-month recognition event. Safety is a year-round cooperative undertaking requiring an ever-present safety consciousness on the part of every employee. Likewise, implementation of the 5S system must extend beyond the initial training and activities conducted this month to make an impact on creating a safer and more efficient workplace.
The 5S activities are the basics. They are not hard to do. But they are hard to do every single day. By embedding 3 key factors into 5S activities, the 5S system will become a long-term best practice rather than a brief experiment.
Make it Meaningful
People have to be motivated to change. Human beings resist change when it is done to them. Human beings accept change when they are involved, and the change is meaningful to them. This is no different with 5S.
Imagine if someone else did 5S for you in your area, throwing things out you have been saving ‘just in case’ and putting your tools in new locations. That would be an unwelcome change. On the other hand, if you were able to take the time to clear out what you did not need, make space to properly locate the items you need, fix the machines so they don’t leak oil, etc. you might feel a lot better about your work space.
We encourage motivation to change by giving employees ownership in the process and letting them create the workspace that best facilitates their productivity. To sustain 5S, it must be meaningful, and people must be motivated to accept the change.
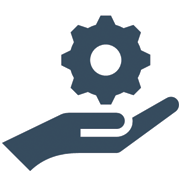
Link to Team Goals
When people see that a simple thing like 5S contributes to meeting their performance goals, they are more likely to value and sustain it. Good 5S reduces set up time and increases output per labor hour so employees should be held accountable and rewarded for consistently following 5S practices.
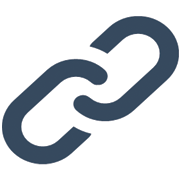
Perform Regular Audits
For some of us, the natural state of our desk or workstation is clutter. It’s human nature to let a little bit of clutter go unnoticed, especially if productivity numbers are good. Many leaders only emphasize cleaning up and looking sharp when customers or executives come through. But disorganization does not contribute to optimal productivity. Use a 5S check list to go through each area at least monthly to ensure 5S compliance and identify areas of improvement.
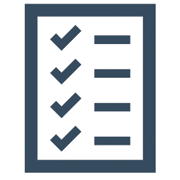