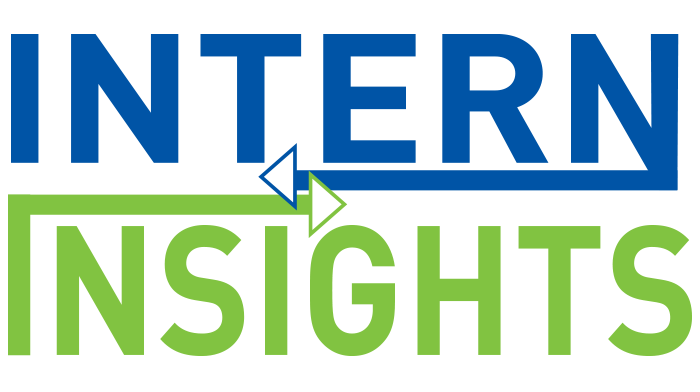
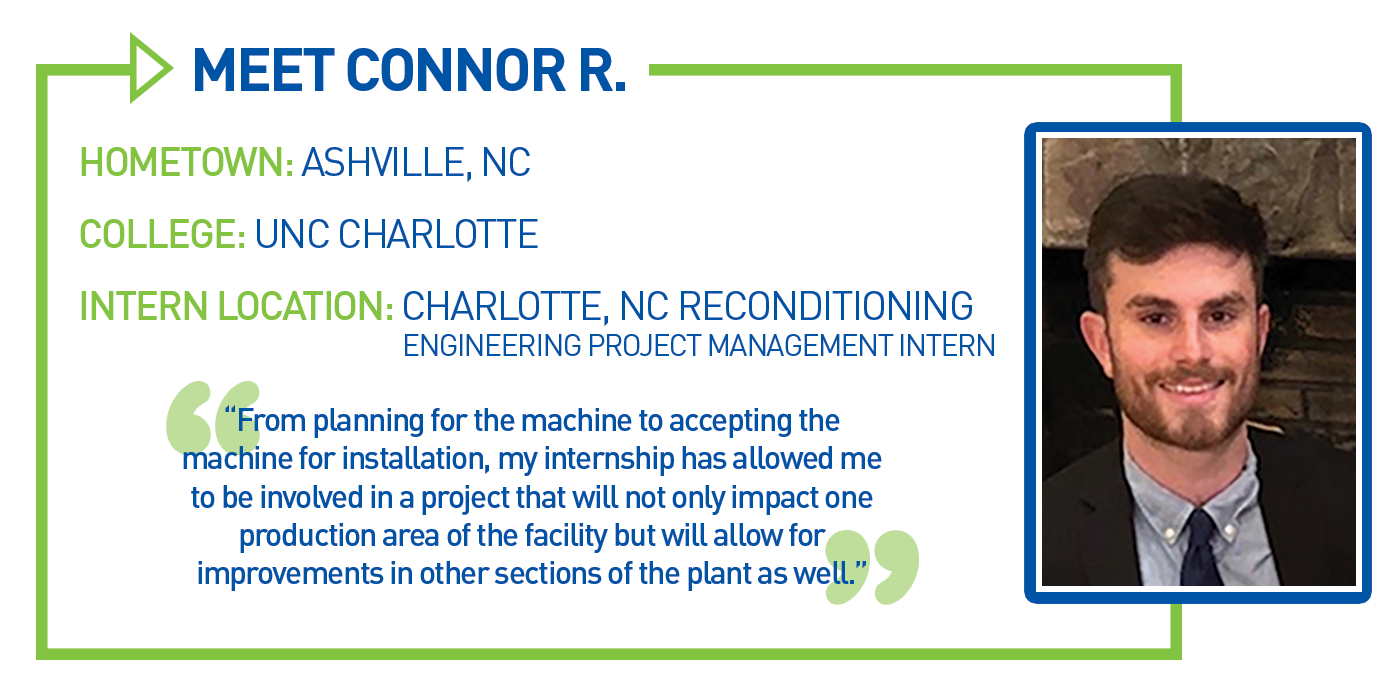
My internship experience at the Charlotte, NC Reco Steel facility has allowed me the opportunity to become a valuable member of the team while assisting with an automation project that will innovate operations.
The automation project I have been working on involves a forming line machine. My primary project duties include coordinating with the remote project engineers to make sure the project is going well, scheduling of tasks, meeting with contractors and vendors to have parts fabricated, and designing parts in AutoCAD to fit the needs of the project. In a normal day, I meet with the project engineer to discuss details of the project, give updates to the plant manager, meet with vendors to discuss machinery that needs to be fabricated, and work on drawings and measurements for project planning. From planning for the machine to accepting the machine for installation, my internship has allowed me to be involved in a project that will not only impact one production area of the facility but will allow for improvements in other sections of the plant as well.
The work that I have been doing is very similar to the type of job I hope to get after school. The office I work in feels like a team and works together to keep the plant running as efficiently as possible. I would describe the work atmosphere as relaxed and friendly. The plant has a strong culture of safety, and everyone is supportive and motivated.
While the operations I am a part of seem to be running smoothly, my only suggestion would be for a quicker design process for designing parts for projects when coordinating with the regional project engineers.
I am thankful for the opportunity to learn about how a plant is run, to understand more about the tasks that a project manager and engineer do daily, and the leadership that have allowed me to obtain a wider view of the career opportunities possible with Mauser Packaging Solutions.
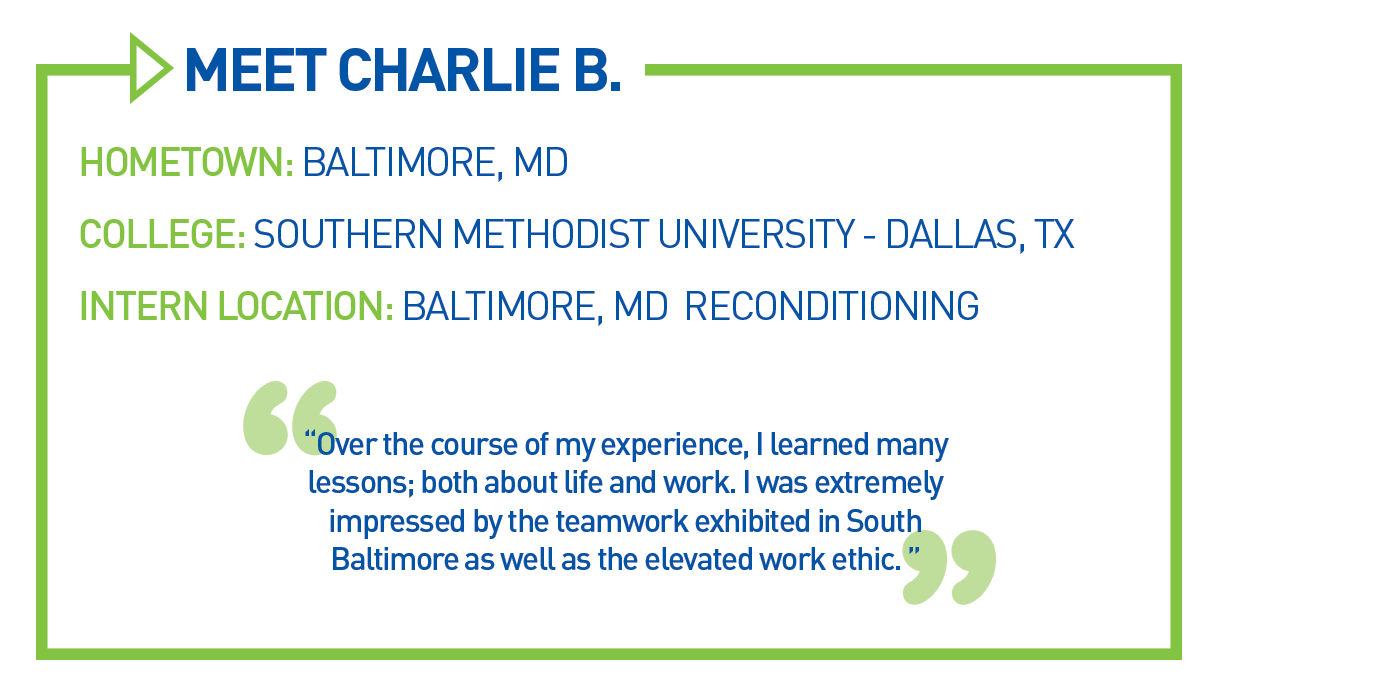
This summer, I had the opportunity to work in the South Baltimore Reco IBC facility. Over the course of my experience, I learned many lessons; both about life and work. When I entered the building for the first time, I was handed a hard hat, eye protection, and steel toed boots before attending my first daily pre-work meeting. After this brief meeting, there was no time wasted once we entered the facility. Every member of the team got straight to their individual jobs and tasks. I was led to a station where I was taught to use a drill to remove caps from the plastic drums. I was instantly overwhelmed by the number of plastic drums that were in front me and believed that rows of drums before me would likely take the entire day to process. However, the rate at which that my co-workers moved was astonishing. Before I knew it, the overwhelming pile in front of me had been conquered.
My responsibilities then expanded to cleaning the drums. Since the plastic drums are not too heavy, you wouldn’t expect this job to be all that difficult, however; this job is exhausting and very physically demanding. The process of cleaning is monotonous, since the process consists of spinning and wiping down the barrel, removing any stickers, and then stacking them on top of one another. Once I was familiar with both the cap removal and washing processes, I learned how to crush different sized drums with the shredding machine.
During my time at the Baltimore facility, I was thoroughly trained by my peer, Anthony. Anthony works every day from 7:00 a.m. to 7:00 p.m., unlike the normal shift hours of 8:00 a.m. to 4:30 p.m. His work ethic was outstanding and inspirational. Instead of taking breaks, he would walk around helping others. Talking and learning from him was a great experience.
From my time at Mauser Packaging Solutions, I think that there are some small things the company could consider to further engage workers. First, small “moral boosters”, small tokens of appreciation like lunch, a t-shirt or hat, to celebrate achievement and recognition; would go a long way in a place where hard work is being done. Likewise, additional investments in cooling fans or equipment would be appreciated by the workers making their jobs safer, easier and allow them to be more productive.
Overall, I was overwhelmed to see how hard employees’ workdays are, day in and day out. I was extremely impressed by the teamwork exhibited in South Baltimore as well as the elevated work ethic. I would recommend that leadership from the depths of the organization spend more time working alongside facility employees to achieve a better sense of the commitment and hard work that is present in the production environment.