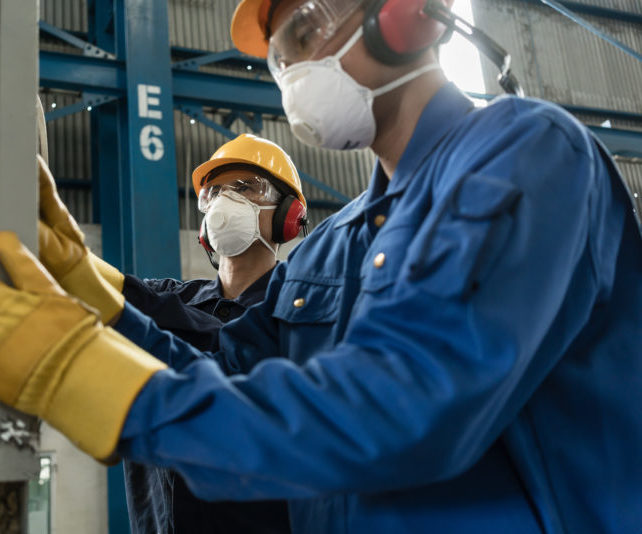
In instances where our supply chains were unable to meet our demand, options outside of the normal purchasing channels were used to procure products and services in a timely manner. Examples include:
- An emergency response cleaning service was secured in mid-March enabling North American facilities to schedule timely service(s). Securing this relationship early on resulted in decreased service lead time.
- Several thousand face coverings were purchased in Europe and shipped to facilities in China, Malaysia, and Singapore. As the pandemic spread, some orders were diverted to the Unites States to bridge the gap until a reliable supply streams could be secured for North American facilities.
- New suppliers were introduced to our network by leveraging our new Indirect Procurement partnership with IBM.
- Our sales teams unlocked new hand sanitizer supplier options from within our customer network. The team worked to identify customers who were converting production lines to meet the skyrocketing global demand for hand sanitizer.
- Centralized warehouses have been established as storage and distribution sites for safety inventory. PPE is warehoused for International locations in Bruehl, Germany while the Anniston, Ala. facility serves as the North American distribution center for more than 650,000 masks.
- In Brazil, Turkey and the Asia-Pacific region, employees were provided with essential care packages including masks, soap, and cleaning products when items were extremely difficult to purchase as an individual within the country/region.
“With the whole world searching for the same PPE supplies, our procurement teams have done a remarkable job securing and obtaining the needed protection for our global organization. Our people have gone above and beyond to make this procurement work,” commented Ivo Franken, Vice President of International Procurement and Logistics.
As we continue to adapt during this pandemic, we have also begun to source supplies and equipment to help monitor the health of our employees.
In addition to encouraging employees to utilize local COVID-19 testing sites, Mauser Packaging Solutions has partnered with VAULT Health to provide onsite and at-home COVID testing. As of July 2020, more than 500 VAULT tests results have been received by Mauser Packaging employees. Test results are typically received in 24-48 hours and help us ensure that we are providing a safe workplace.
Automated temperature screening devices are being piloted in select North American and European facilities to ensure that all facilities are utilizing accurate and efficient devices. During the pilot, data and feedback are being compiled to compare functionality, accuracy, ease of setup and use, technological capability, and the ability for future integration with existing systems. Following the pilot, a standard automated temperature device will be rolled out to all facilities.
As COVID-19 continues to change the needs of our facilities and re-shape what our normal work environment looks like, our facilities and our people continue prove our resiliency and creativity in finding resourceful solutions to the challenges that arise. “Our ability to ensure our facilities and offices of all sizes have the supplies and resources needed to protect our employees while remaining operational is a testament to the advantages of our ‘One Mauser’ culture,” commented Bharat Sharma, Vice President of North American Procurement.