Better time usage
Getting rid of unwanted materials and organizing important tools and supplies eliminates clutter and confusion.
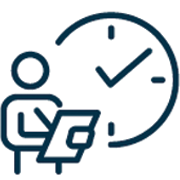
Less Wasted Space
Eliminating unnecessary material stockpiles and consolidating tool storage will clear up room for more useful applications.
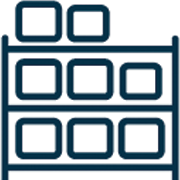
Reduced Injury Rates
Organizing work areas for efficiency and ease of use will reduce the movements needed for workers to do their jobs. Removing clutter and routinely cleaning up spills will eliminate trip hazards. As a result, workers will experience less fatigue and fewer injuries.
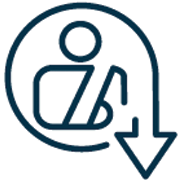
Reduced Equipment Downtime
When tools and equipment are kept clean, routinely inspected, and used in a standardized way, preventative maintenance is much easier, and major failures can often be prevented entirely.
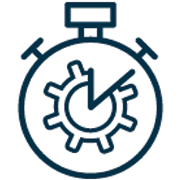
Improved Consistency and quality
Standardizing work processes will reduce variations and mistakes. By eliminating faults and failures, overall productivity can be dramatically improved.
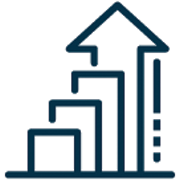
Heightened Employee Moral
When 5S principles are used effectively, workers see that their input is valued, and their performance is recognized. This creates an environment where workers can feel pride in their work and take an interest in improving their company.
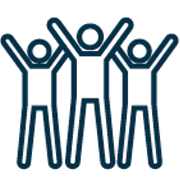
5S is an ongoing and sustained improvement in how you organize your workplace. One of the most important parts of 5S is that of standardizing work. Standardization provides a firm foundation on which all other improvements can be built. Until there is a repeatable and stable process, it is hard to understand what is causing problems and there is no way to ensure that improvements will make a difference or even remain effective.
Simple documents to define how work should be performed (Standard Operating Procedures (SOPs) or Work Instructions) can be created very simply using standard word processing packages and pictures ensuring that everyone knows exactly the best method for conducting an operation. This will reduce differences between shifts and different operators as well as giving something that can be improved on. By documenting situations and standardizing, facilities can show actual, measured 5S benefits and improvements.