In-mold labeling combines the molding and decoration processes for more efficient pail production. IML reduces production time by allowing pails to be palletized immediately after molding and eliminating long cooling conveyers and ink drying time. Additionally, the IML machine features a loading magazine that facilitates the quick change of labels from one job to another while the machine is running, reducing changeover and machine downtime. From a safety perspective, IML removes cumbersome ergonomics and manual operation required for the current off set printing or heat transfer label (HTL) processes. It also eliminates a potential burn hazard caused by extreme temperatures used in HTL. When a label SKU is changed, it’s done in an area guarded to prevent injury to our workforce.
To prepare for the change to IML, the Cedar City facility replaced an older injection molding machine and coupled the new machine with an in-mold labeling machine. Customer approval for the new labeling option was coordinated by the operations and sales teams while the technical team at the plant worked to ensure a successful start-up. Employees spent many months testing, training, and becoming comfortable with the new technology before production began.
“This is a great milestone for Mauser Packaging Solutions. This is a path forward and paves the way to leverage this technology for future projects. It’s a huge win for the Cedar City plant and all the team members there,” commented Stephan Dechert, Product Segment Director – North American Small Packaging.
"This is a path forward and paves the way to leverage this technology for future projects."
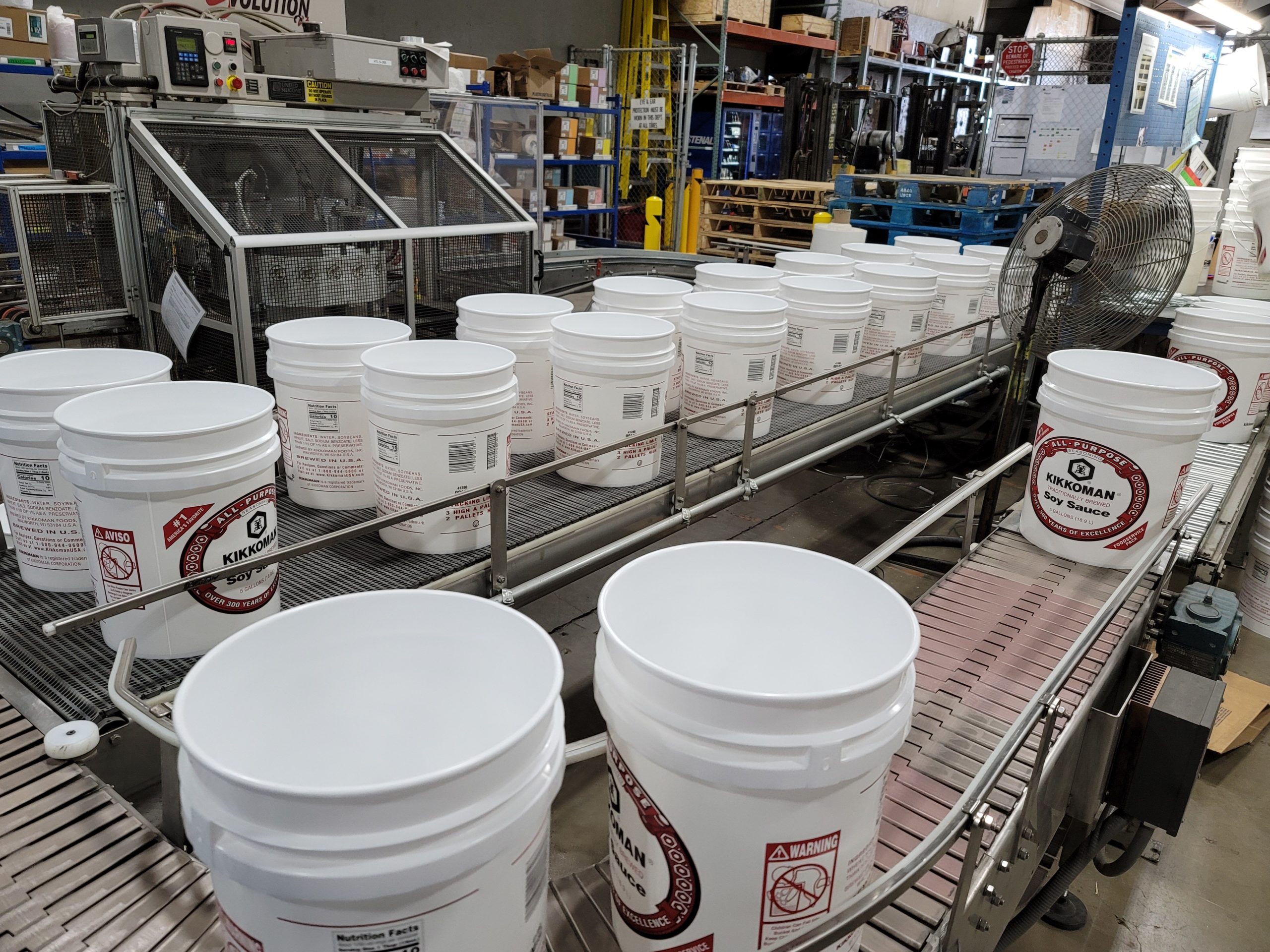

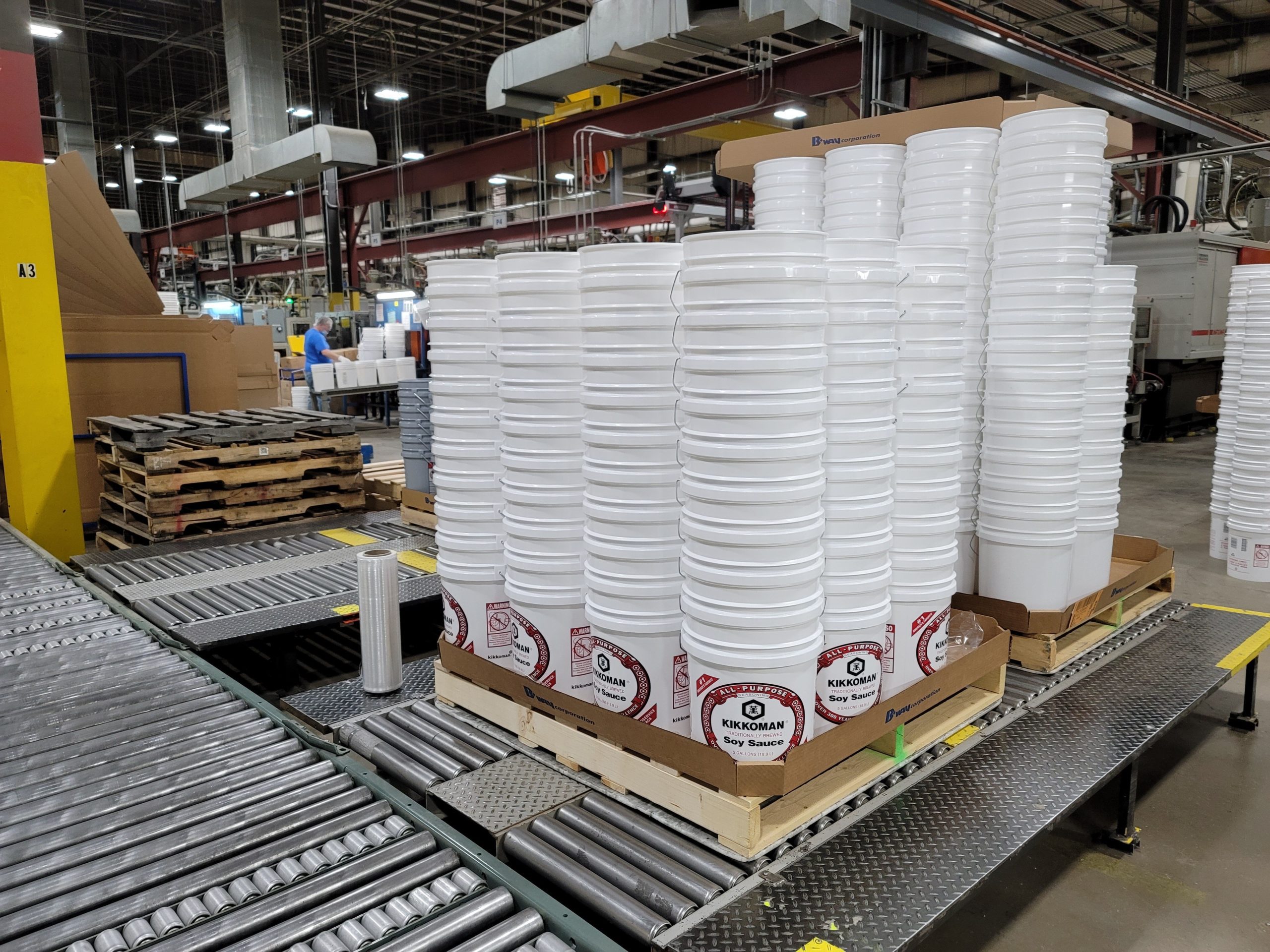