The Hamburg, Germany facility has experienced a positive safety trend since 2021. After having 7 incidents in 2020, the facility reduced the number of incidents by half for the following two years. A single incident in 2022 currently stands as the last incident at the facility.
Improving overall safety at the facility was a step-by- step process that required considerable effort and commitment. Improvement has been achieved through intensive training initiatives (Fullmark), acquisition of new safety equipment, and optimization of work processes. Multiple incidents in 2020 provided opportunities for the facilities to identify risk areas and implement infrastructure and process modification to make the facility a safer workplace in the future.
Incident #1:
Following a forklift incident, infrastructure improvements were implemented including to ensure clear visibility of vehicle versus pedestrian traffic areas:
- Addition and/or improvement of markings for forklift truck and road vehicle driveways
- Instillation of outdoor lighting
- Re-painted footpath markings
These upgrades led to a significant improvement in outdoor safety and emphasized the importance of ensuring that markings in all work areas are always clearly visible.
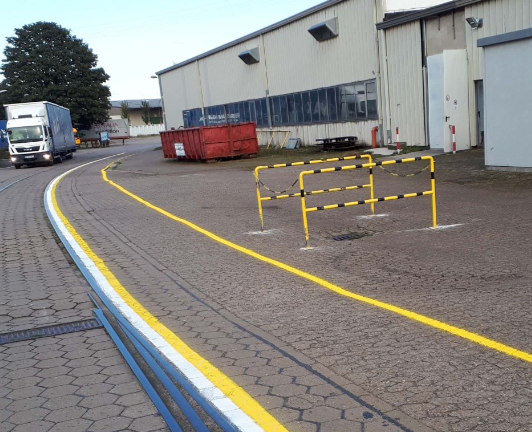
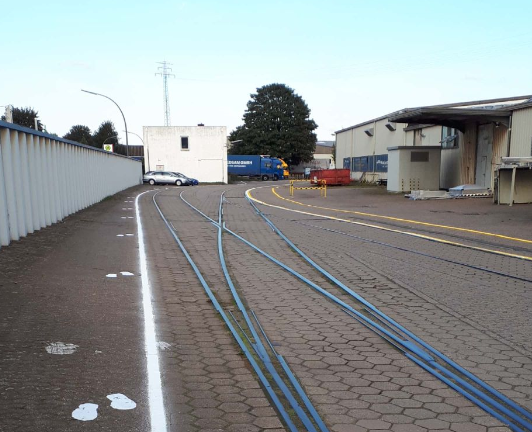
Incident #2:
After an operator sustained a cut from a knife during a quality inspection, normal knives were replaced with safety knives and the quality process was modified. With the new quality inspection process, containers are examined using illumination instead of cutting. This eliminates the use of knives which significantly reduces risk during quality inspections.
In addition to making quality inspections safer, this process also results in material savings and product preservation by eliminating a non-destructive method of examination.
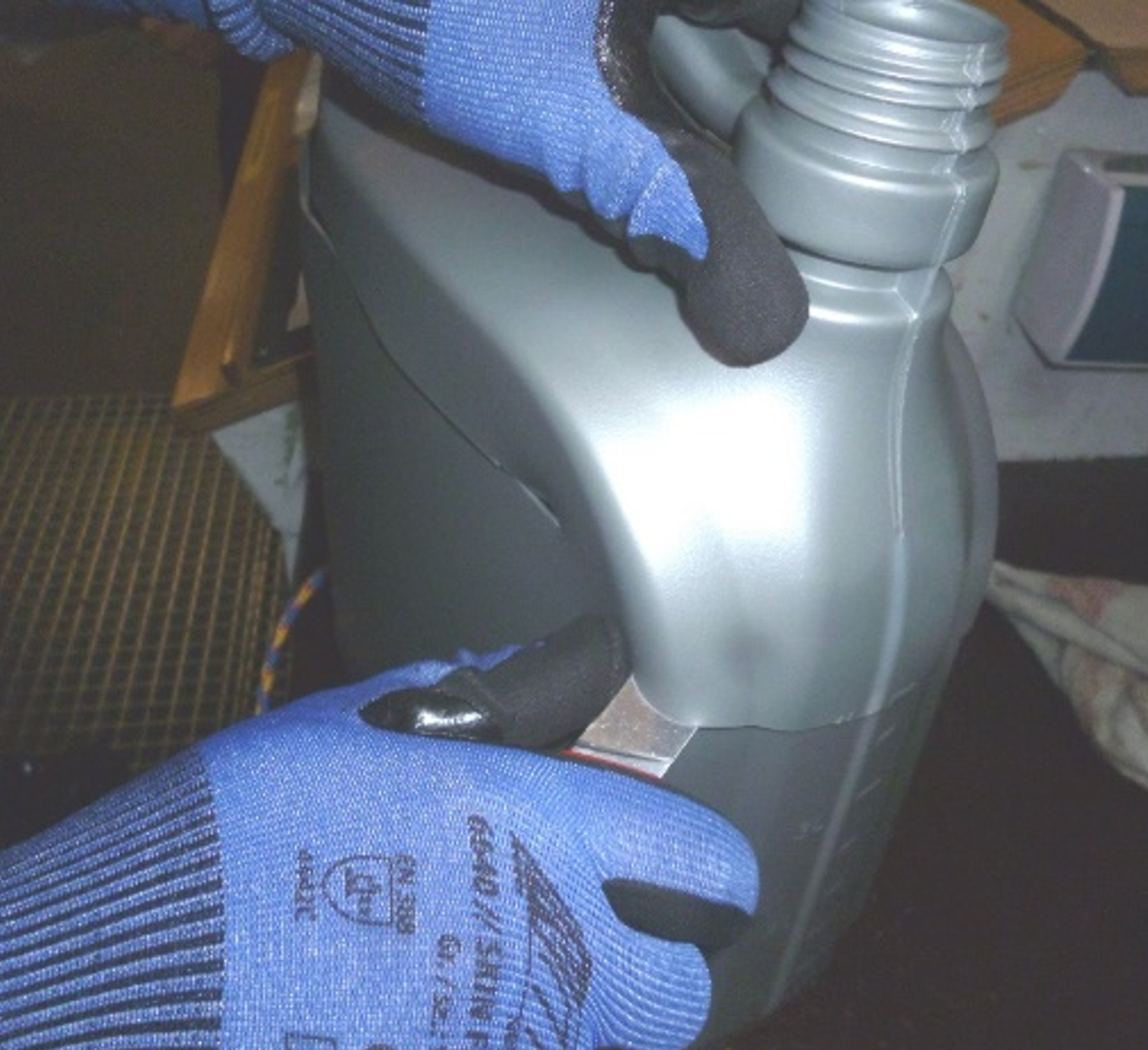
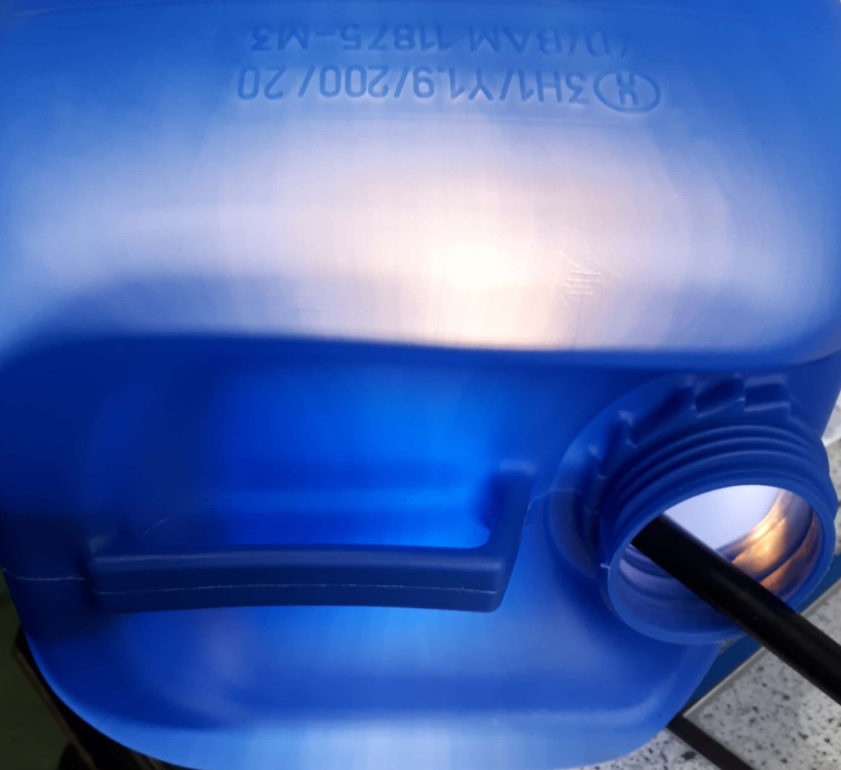
“Both situations represent the importance of using safety incidents as opportunities for learning and improvement. While we never want to wait on an incident to make safety modifications, we can always learn from these incidents and use them as motivation to work safer in the future.”